How Johnson Controls Slashed Field Time by 50% — Without Adding Headcount
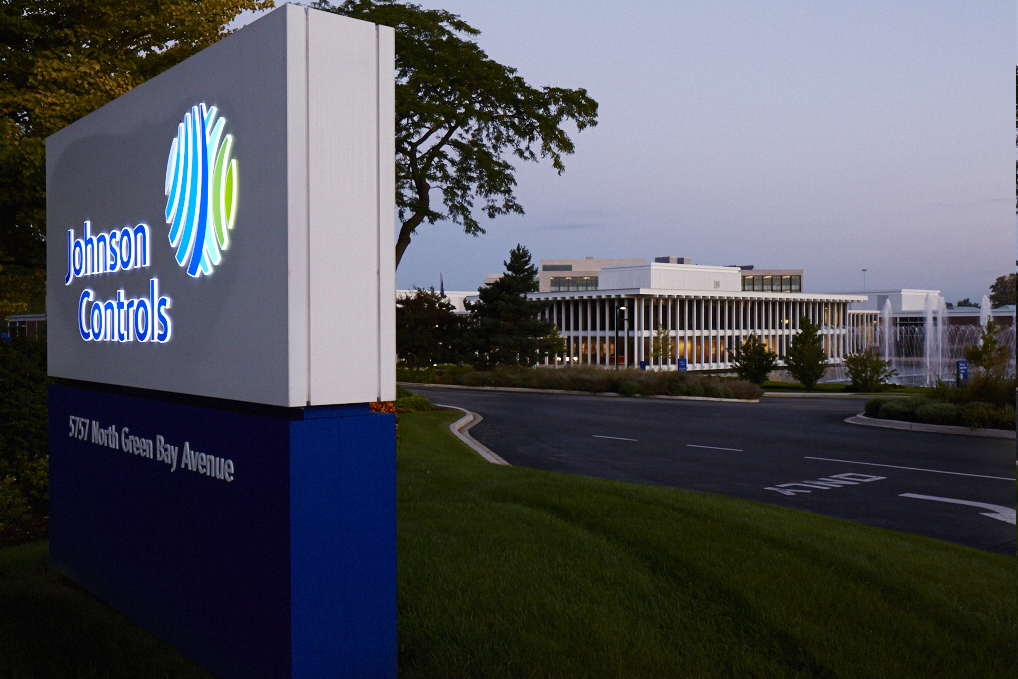
What enterprise teams can learn from the world's largest fire & security company
If you’re running a field-heavy operation, you know the truth:
You don’t get do-overs.
Miss a detail? You're back on-site.
Lose track of your process? Expect rework.
Still using paper? You’re leaking profit.
That’s why Johnson Controls Integrated Fire & Security turned to ArcSite.
These aren’t weekend warriors. They’re professionals servicing Fortune 500 clients across 50+ countries. They don’t have time for guesswork or patience for duct-taped workflows.
Here’s how their Global Centre of Excellence scaled smarter site surveys across the UK and Ireland.
The Problem: One Site Visit, One Shot
JCI’s surveyors aren’t just measuring walls. They’re documenting fire systems, CCTV placements, access control, and emergency lighting across complex commercial spaces.
They get one chance to collect everything.
No margin for error. No second site visit.
Before ArcSite:
- Paper drawings
- Manual markups
- Hours wasted redrawing in AutoCAD
- Photos in separate folders
- Survey data that lived (and died) on someone’s desktop
The ArcSite Difference:
✅ 50% faster surveys
✅ One app, full workflow
✅ CAD-ready outputs—no redraws
✅ Enterprise standardization at scale
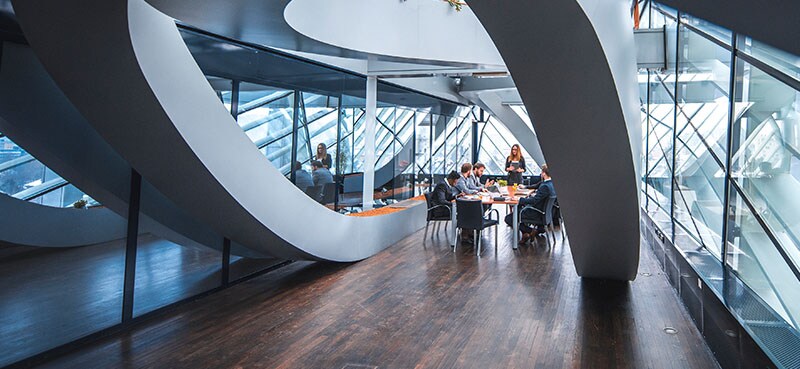
5 Enterprise-Level Problems ArcSite Solved
1. One Surveyor, Many Systems = High Risk
Johnson Controls shifted from having multiple system-specific surveyors on-site… to just one covering everything.
That saves time and cost, but it only works if the surveyor can still deliver expert-level documentation across fire, security, CCTV, access control, and more.
With ArcSite:
Surveyors like Alastair capture annotated drawings, pin photos directly to locations, and share everything with specialists back at HQ. The result?
- Remote collaboration, built into the workflow
- No second visits just to clarify details
- Design-ready documentation that gets signed off with speed and confidence
“More and more, the engineering side of things is being done remotely… [ArcSite] eliminates doubt.”
— Simon Revell, Installation Engineer
2. Data Collection = Double Entry (And Double the Mistakes)
Before ArcSite, surveyors like Alastair filled out paper drawings, then recreated everything back at their desks in Autodesk.
Sound familiar?
It’s not just inefficient. It’s error-prone. And it doesn’t scale.
With ArcSite:
Draw once, in the field, on an iPad. Capture data, annotations, and images as you walk the site. Export to CAD without touching a mouse.
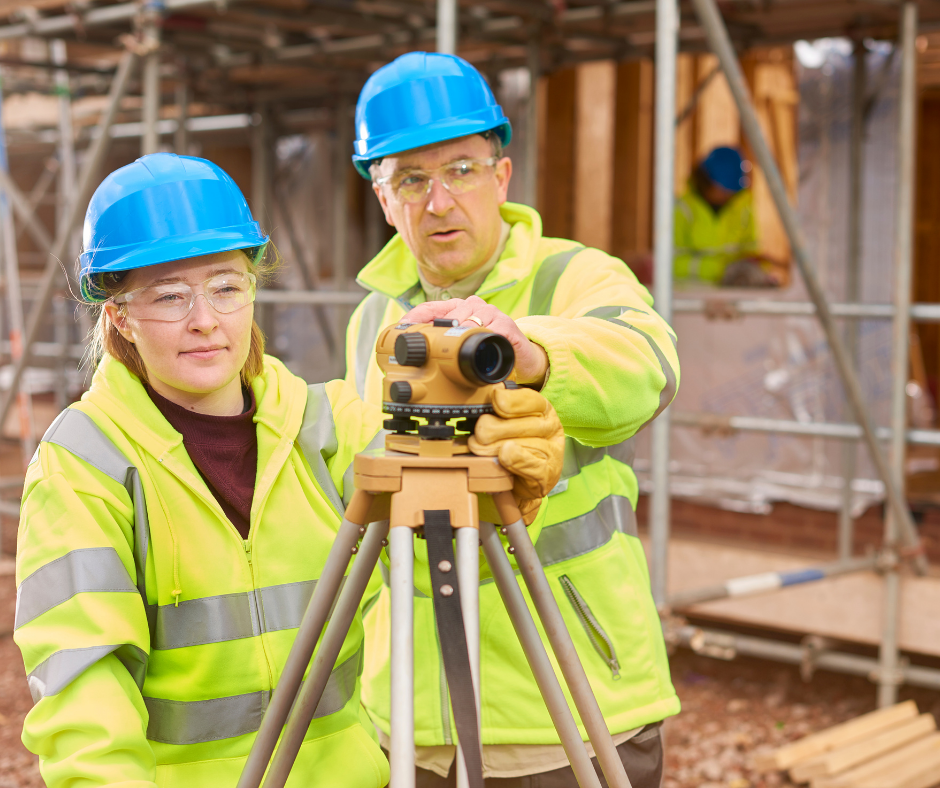
3. Paper Is a Dead End
Photos of sketches. Emails with redlines. PDFs scanned from napkins.
Designers were piecing together plans from inconsistent files and chasing surveyors for clarity.
With ArcSite:
- Instant cloud sharing
- Scaled, layered PDFs
- Clean handoff to Design
- Version control baked in
4. Everyone Gets the Same Drawing—Whether They Need It or Not
Need to send just the electrical plan to a subcontractor? Tough luck. Before ArcSite, they’d either send everything or create duplicate files.
With ArcSite:
They share specific layers, views, or notes depending on the audience. No extra work. No oversharing. No confusion.
5. Scaling Standardization Across 50+ Fortune 500 Clients
JCI’s Birmingham COE has grown 300% since 2010. They needed a system that matched that scale.
With ArcSite, they built custom libraries and reusable symbols, so every survey, across every site, starts from the same professional baseline.
“In my opinion, we’ll be more productive in the long term. No better program for our line of work.”
— Paul Gibson, Surveyor
What Enterprise Teams Really Value
Scaled Drawings
Precision meets compliance. ArcSite outputs pass muster with CAD teams, inspectors, and installers.
Embedded Photos
Every image is pinned to the plan. Less ambiguity. Faster approvals.
Custom Shape Libraries
Create once. Reuse across the entire org. Faster delivery. Less training.
Peer Collaboration
Design, Ops, and Field teams all speak the same visual language now.
The Results
- 50% time savings in the field
- Zero rework from illegible notes or incorrect CAD redraws
- Faster handoffs to the design team
- Cleaner documentation for audits, compliance, and install crews
Scaling Your Field Ops? Start Here.
You’re not just winning jobs, you’re building a system that wins repeatedly.
ArcSite helps your team:
- Quote faster
- Survey smarter
- Deliver clean documentation—without chasing field crews or fixing drawings
Get a custom walkthrough to see how your field team can gain back 50% of their time, starting next week.
How JES Foundation Repair Scaled Sales, Accuracy, and Trust with ArcSite
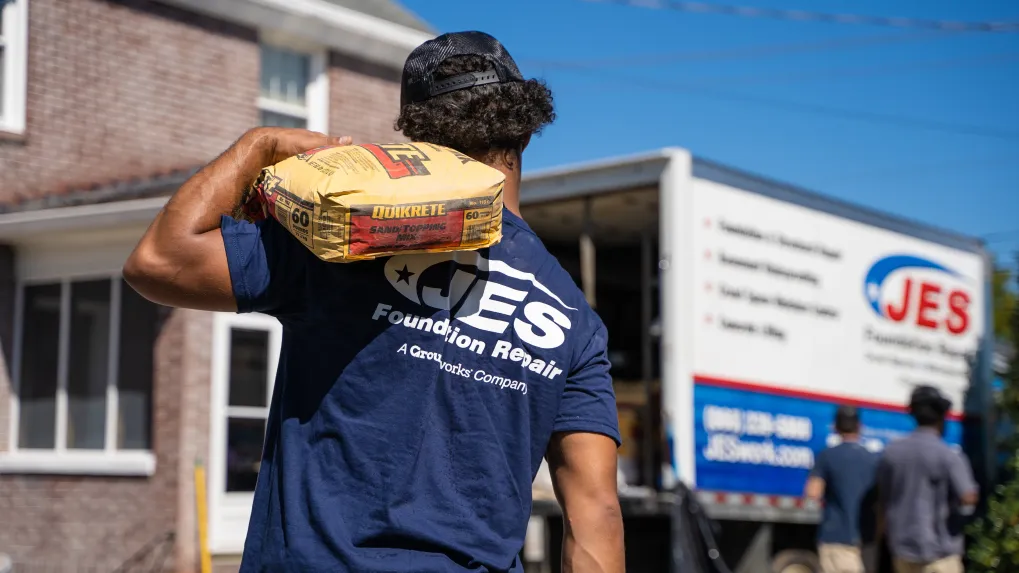
From back-of-the-napkin sketches to professional-grade proposals—all from the job site.
The Company: JES Foundation Repair
Founded in 1993, JES Foundation Repair, now part of Groundworks, the nation’s largest privately held foundation services company, has served more than 70,000 customers across the Mid-Atlantic, including Virginia, Maryland, Washington, D.C., and North Carolina. With four regional offices and an in-house team of licensed Professional Engineers, JES is one of the few foundation repair companies with licensed Professional Engineers on staff, giving them the ability to certify structural work without relying on outside firms.
Their specialties include:
- Foundation repair and stabilization
- Crawl space encapsulation
- Basement waterproofing
- Concrete lifting and leveling
The Problem: Paper Plans, Digital Expectations
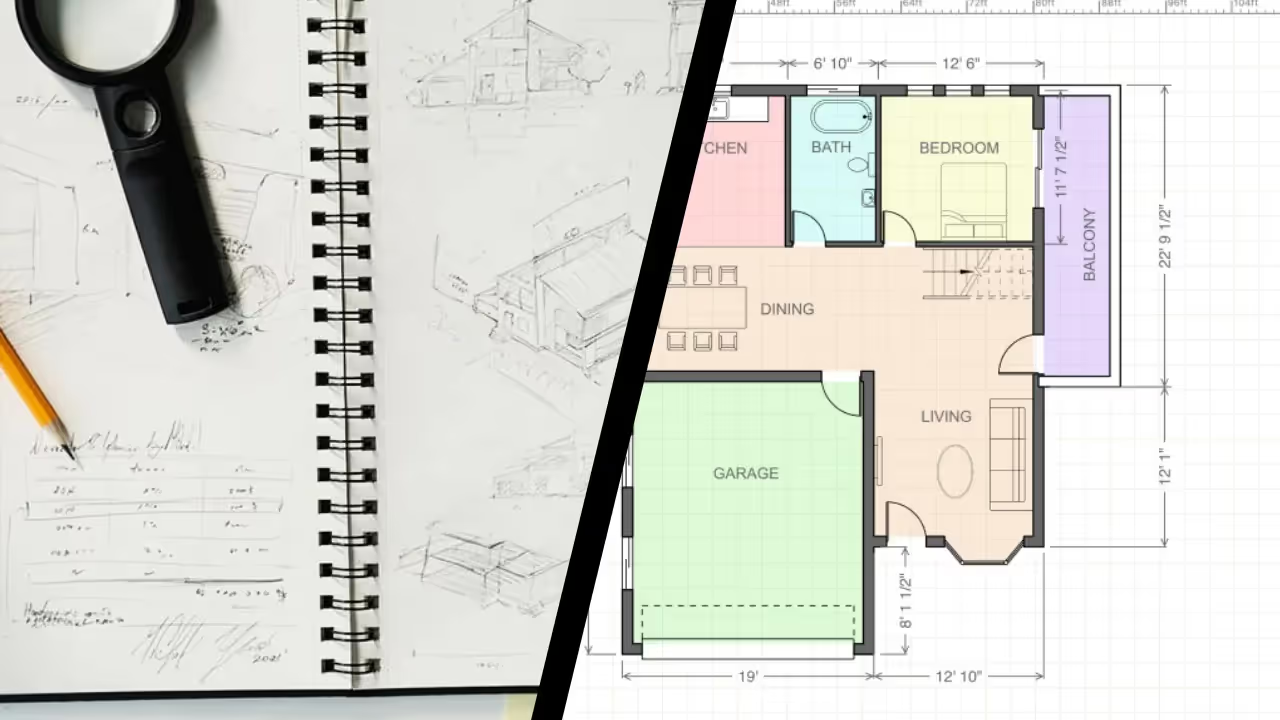
In a business where accuracy equals safety, traditional pen-and-paper drawings were holding JES back.
Here’s why:
- Grid paper isn’t precise. Measuring and sketching “2.3 feet” is tough when each box equals 2 feet.
- Rework was mandatory. Every field sketch had to be redrawn in desktop software at the office, which added time, cost, and increased the risk of errors.
- Their software didn’t scale. The engineers’ CAD-style tools were clunky, hard to use in the field, and not designed for real-world construction conditions.
- Customer perception lagged behind. Paper plans and generic proposals didn’t reflect the professionalism or precision JES engineers were delivering behind the scenes.
They needed a faster and more accurate way to bridge the gap between the field and the office, without sacrificing professionalism or precision.
“In my first year, I sold over two million dollars worth of product – and I literally could never have done this job without ArcSite.”
– Collin Dozier, Certified Field Inspector, JES Foundation Repair
The Solution: ArcSite
JES adopted ArcSite to bring mobile-first precision to their sales and engineering workflows.
Here’s what changed:
- Field drawings got real. ArcSite allowed reps to draw to scale onsite using just a tablet—no paper, no rework, no CAD.
- Measurements became intelligent. Reps could calculate square footage instantly and generate insulation or repair estimates based on wall height, site photos, and notes.
- Communication became seamless. Photos, drawings, and annotations were synced in real-time between the field and office, reducing back-and-forth and costly errors.
- Every rep looked like a pro. Drawings were clean, professional, and permit-ready, helping build trust with homeowners and increase close rates.
Enterprise-Grade Results
Accuracy That Engineers Approve
ArcSite’s precision tools helped JES eliminate estimation errors and field-to-office miscommunications. The app’s scaled drawings are accurate enough to use in permitting—no redraws required.
Time Savings that Add Up
With ArcSite, reps collect site data once, on-site, and send it straight into the workflow. No more drawing once in the field and again at the office. No more delays due to weather, messy paper, or missing measurements.
Ease of Use in the Real World
Designed for the way contractors actually work, ArcSite functions in crawlspaces, basements, and rough conditions—anywhere the job takes them.
Customer Confidence, Built-In
Reps present clean, accurate, and visual proposals on the spot, helping customers understand the problem, see the solution, and say “yes” faster.
The Takeaway:
JES didn’t just adopt a drawing app. They operationalized a system for field accuracy, engineering trust, and sales growth.
“ArcSite lets us deliver field-ready precision, office-grade accuracy, and customer-ready proposals—all from one platform.”
– Collin Dozier, Certified Field Inspector, JES Foundation Repair
Whether you're running a $1M business or a $100M operation, the lesson from JES is clear:
If your team still relies on paper in the field, you’re leaving money—and trust—on the table.
Why Enterprise Contractors Are Adopting Tools Like ArcSite
Enterprise foundation repair and construction companies aren’t just looking for sketch tools—they need scalable solutions that streamline proposals, accelerate takeoffs, and reduce rework across every region and rep. When your team operates at scale, even small inefficiencies in drawing or estimating compound into major costs. ArcSite empowers field teams to generate accurate, visual takeoffs and polished proposals onsite, eliminating the back-and-forth between paper sketches, spreadsheets, and office redrawing. The result? Faster approvals, higher close rates, and standardized workflows your leadership team can trust.
Get a custom walkthrough to see how your field team cut proposals time, eleiminate redraws, and close more deal–starting next week.
JES Case Study
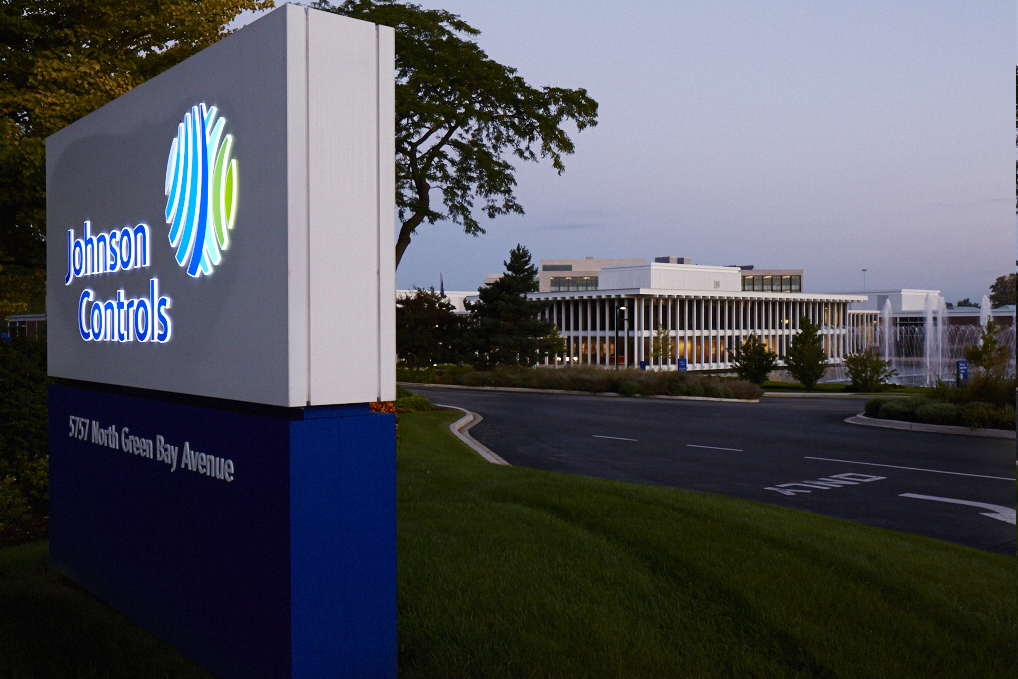
What enterprise teams can learn from the world's largest fire & security company
If you’re running a field-heavy operation, you know the truth:
You don’t get do-overs.
Miss a detail? You're back on-site.
Lose track of your process? Expect rework.
Still using paper? You’re leaking profit.
That’s why Johnson Controls Integrated Fire & Security turned to ArcSite.
These aren’t weekend warriors. They’re professionals servicing Fortune 500 clients across 50+ countries. They don’t have time for guesswork or patience for duct-taped workflows.
Here’s how their Global Centre of Excellence scaled smarter site surveys across the UK and Ireland.
The Problem: One Site Visit, One Shot
JCI’s surveyors aren’t just measuring walls. They’re documenting fire systems, CCTV placements, access control, and emergency lighting across complex commercial spaces.
They get one chance to collect everything.
No margin for error. No second site visit.
Before ArcSite:
- Paper drawings
- Manual markups
- Hours wasted redrawing in AutoCAD
- Photos in separate folders
- Survey data that lived (and died) on someone’s desktop
The ArcSite Difference:
✅ 50% faster surveys
✅ One app, full workflow
✅ CAD-ready outputs—no redraws
✅ Enterprise standardization at scale
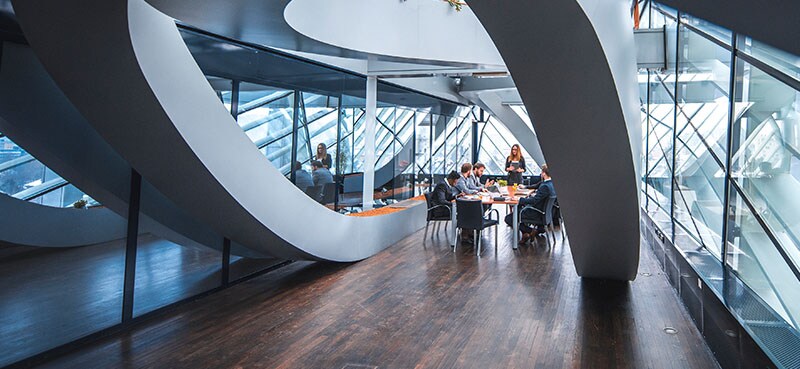
5 Enterprise-Level Problems ArcSite Solved
1. One Surveyor, Many Systems = High Risk
Johnson Controls shifted from having multiple system-specific surveyors on-site… to just one covering everything.
That saves time and cost, but it only works if the surveyor can still deliver expert-level documentation across fire, security, CCTV, access control, and more.
With ArcSite:
Surveyors like Alastair capture annotated drawings, pin photos directly to locations, and share everything with specialists back at HQ. The result?
- Remote collaboration, built into the workflow
- No second visits just to clarify details
- Design-ready documentation that gets signed off with speed and confidence
“More and more, the engineering side of things is being done remotely… [ArcSite] eliminates doubt.”
— Simon Revell, Installation Engineer
2. Data Collection = Double Entry (And Double the Mistakes)
Before ArcSite, surveyors like Alastair filled out paper drawings, then recreated everything back at their desks in Autodesk.
Sound familiar?
It’s not just inefficient. It’s error-prone. And it doesn’t scale.
With ArcSite:
Draw once, in the field, on an iPad. Capture data, annotations, and images as you walk the site. Export to CAD without touching a mouse.
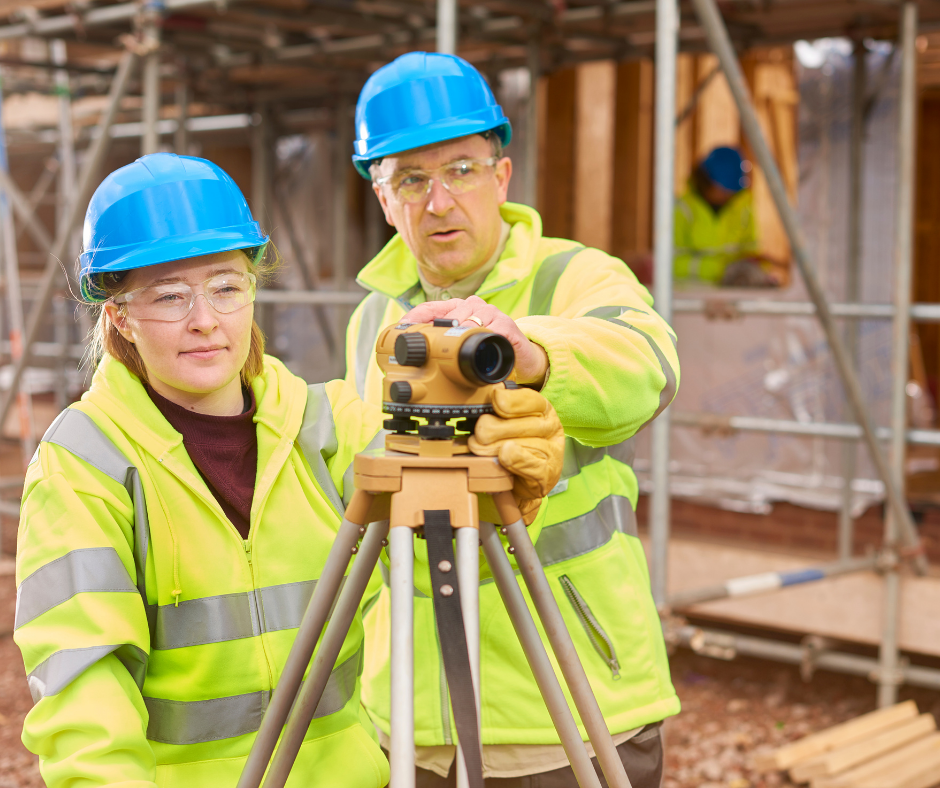
3. Paper Is a Dead End
Photos of sketches. Emails with redlines. PDFs scanned from napkins.
Designers were piecing together plans from inconsistent files and chasing surveyors for clarity.
With ArcSite:
- Instant cloud sharing
- Scaled, layered PDFs
- Clean handoff to Design
- Version control baked in
4. Everyone Gets the Same Drawing—Whether They Need It or Not
Need to send just the electrical plan to a subcontractor? Tough luck. Before ArcSite, they’d either send everything or create duplicate files.
With ArcSite:
They share specific layers, views, or notes depending on the audience. No extra work. No oversharing. No confusion.
5. Scaling Standardization Across 50+ Fortune 500 Clients
JCI’s Birmingham COE has grown 300% since 2010. They needed a system that matched that scale.
With ArcSite, they built custom libraries and reusable symbols, so every survey, across every site, starts from the same professional baseline.
“In my opinion, we’ll be more productive in the long term. No better program for our line of work.”
— Paul Gibson, Surveyor
What Enterprise Teams Really Value
Scaled Drawings
Precision meets compliance. ArcSite outputs pass muster with CAD teams, inspectors, and installers.
Embedded Photos
Every image is pinned to the plan. Less ambiguity. Faster approvals.
Custom Shape Libraries
Create once. Reuse across the entire org. Faster delivery. Less training.
Peer Collaboration
Design, Ops, and Field teams all speak the same visual language now.
The Results
- 50% time savings in the field
- Zero rework from illegible notes or incorrect CAD redraws
- Faster handoffs to the design team
- Cleaner documentation for audits, compliance, and install crews
Scaling Your Field Ops? Start Here.
You’re not just winning jobs, you’re building a system that wins repeatedly.
ArcSite helps your team:
- Quote faster
- Survey smarter
- Deliver clean documentation—without chasing field crews or fixing drawings
Get a custom walkthrough to see how your field team can gain back 50% of their time, starting next week.
JES Case Study
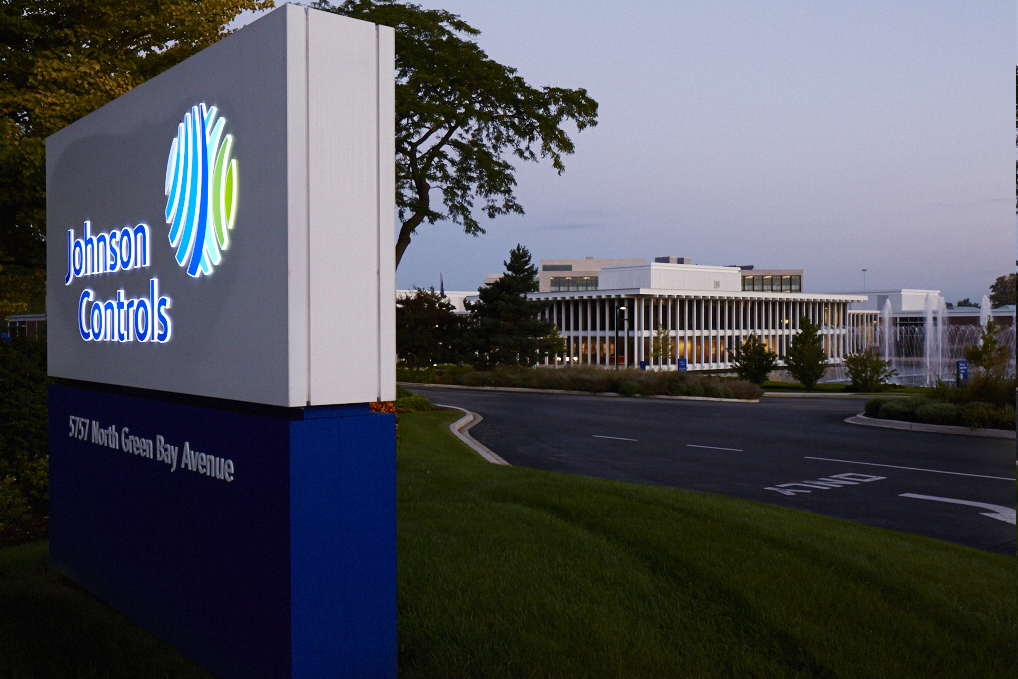
What enterprise teams can learn from the world's largest fire & security company
If you’re running a field-heavy operation, you know the truth:
You don’t get do-overs.
Miss a detail? You're back on-site.
Lose track of your process? Expect rework.
Still using paper? You’re leaking profit.
That’s why Johnson Controls Integrated Fire & Security turned to ArcSite.
These aren’t weekend warriors. They’re professionals servicing Fortune 500 clients across 50+ countries. They don’t have time for guesswork or patience for duct-taped workflows.
Here’s how their Global Centre of Excellence scaled smarter site surveys across the UK and Ireland.
The Problem: One Site Visit, One Shot
JCI’s surveyors aren’t just measuring walls. They’re documenting fire systems, CCTV placements, access control, and emergency lighting across complex commercial spaces.
They get one chance to collect everything.
No margin for error. No second site visit.
Before ArcSite:
- Paper drawings
- Manual markups
- Hours wasted redrawing in AutoCAD
- Photos in separate folders
- Survey data that lived (and died) on someone’s desktop
The ArcSite Difference:
✅ 50% faster surveys
✅ One app, full workflow
✅ CAD-ready outputs—no redraws
✅ Enterprise standardization at scale
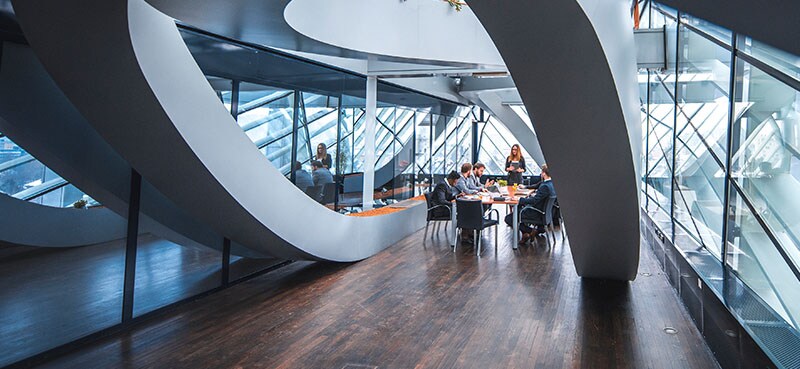
5 Enterprise-Level Problems ArcSite Solved
1. One Surveyor, Many Systems = High Risk
Johnson Controls shifted from having multiple system-specific surveyors on-site… to just one covering everything.
That saves time and cost, but it only works if the surveyor can still deliver expert-level documentation across fire, security, CCTV, access control, and more.
With ArcSite:
Surveyors like Alastair capture annotated drawings, pin photos directly to locations, and share everything with specialists back at HQ. The result?
- Remote collaboration, built into the workflow
- No second visits just to clarify details
- Design-ready documentation that gets signed off with speed and confidence
“More and more, the engineering side of things is being done remotely… [ArcSite] eliminates doubt.”
— Simon Revell, Installation Engineer
2. Data Collection = Double Entry (And Double the Mistakes)
Before ArcSite, surveyors like Alastair filled out paper drawings, then recreated everything back at their desks in Autodesk.
Sound familiar?
It’s not just inefficient. It’s error-prone. And it doesn’t scale.
With ArcSite:
Draw once, in the field, on an iPad. Capture data, annotations, and images as you walk the site. Export to CAD without touching a mouse.
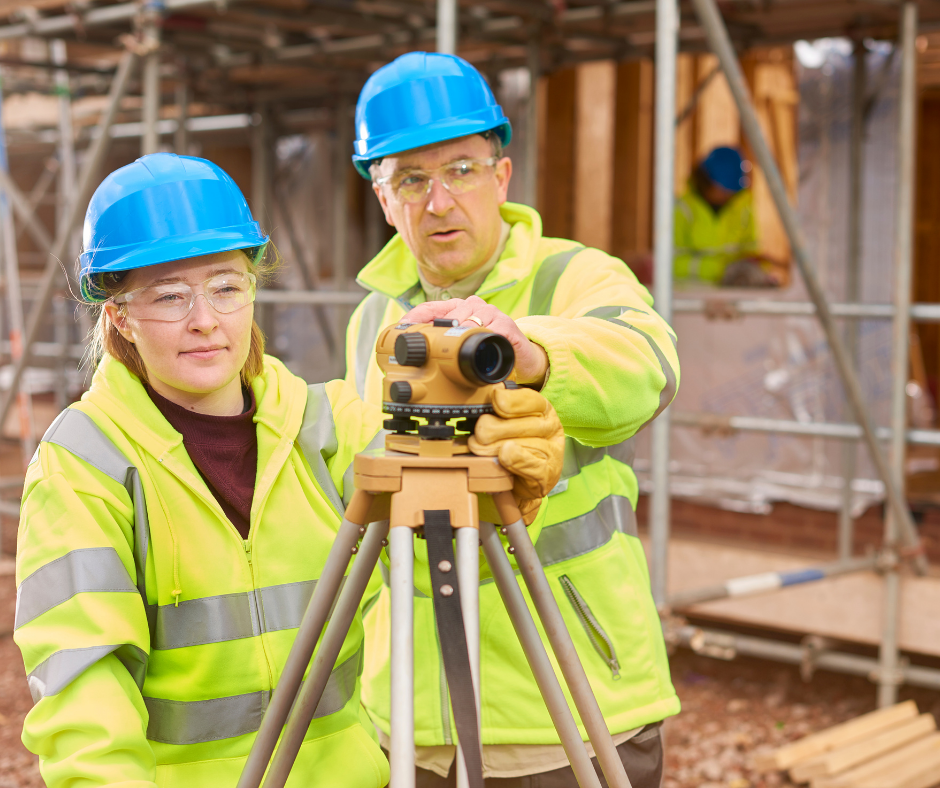
3. Paper Is a Dead End
Photos of sketches. Emails with redlines. PDFs scanned from napkins.
Designers were piecing together plans from inconsistent files and chasing surveyors for clarity.
With ArcSite:
- Instant cloud sharing
- Scaled, layered PDFs
- Clean handoff to Design
- Version control baked in
4. Everyone Gets the Same Drawing—Whether They Need It or Not
Need to send just the electrical plan to a subcontractor? Tough luck. Before ArcSite, they’d either send everything or create duplicate files.
With ArcSite:
They share specific layers, views, or notes depending on the audience. No extra work. No oversharing. No confusion.
5. Scaling Standardization Across 50+ Fortune 500 Clients
JCI’s Birmingham COE has grown 300% since 2010. They needed a system that matched that scale.
With ArcSite, they built custom libraries and reusable symbols, so every survey, across every site, starts from the same professional baseline.
“In my opinion, we’ll be more productive in the long term. No better program for our line of work.”
— Paul Gibson, Surveyor
What Enterprise Teams Really Value
Scaled Drawings
Precision meets compliance. ArcSite outputs pass muster with CAD teams, inspectors, and installers.
Embedded Photos
Every image is pinned to the plan. Less ambiguity. Faster approvals.
Custom Shape Libraries
Create once. Reuse across the entire org. Faster delivery. Less training.
Peer Collaboration
Design, Ops, and Field teams all speak the same visual language now.
The Results
- 50% time savings in the field
- Zero rework from illegible notes or incorrect CAD redraws
- Faster handoffs to the design team
- Cleaner documentation for audits, compliance, and install crews
Scaling Your Field Ops? Start Here.
You’re not just winning jobs, you’re building a system that wins repeatedly.
ArcSite helps your team:
- Quote faster
- Survey smarter
- Deliver clean documentation—without chasing field crews or fixing drawings
Get a custom walkthrough to see how your field team can gain back 50% of their time, starting next week.